THE 9 STEPS OF PRODUCT DEVELOPMENT
- Jason Hugenroth
- Jan 21, 2021
- 3 min read
Updated: Oct 26, 2021

Successfully developing and ultimately launching a product can often make or break a business. Mistakes and wrong turns can easily bankrupt a startup. Even large well-established companies have been sunk by poorly executed product development projects.
The process of developing and commercializing a new or improved physical product is fairly consistent across technologies and industries. Whether developing a potato peeler or new engine technology the following steps still apply.

1 - CONCEPT DEVELOPMENT
A new product or technology is intended to provide a better solution to a problem. Once the problem has been identified, development begins with creating concepts to solve the problem.
This step is also referred to as ideation.

2 - ANALYSIS
The analysis, or research stage, of the project sheds light on the technical uncertainties permeating the early stages of development. Various forms of engineering expertise are employed to eliminate these uncertainties.
Analysis is used to answer a wide range of project specific questions.
For example:
“What materials should be used?
"What will the size and weight be?"
"How much power is required?”
In some cases, questions of technical feasibility will need to be researched.
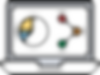
3 - DESIGN
From initial sketches or mental images, detailed design of the physical components of the system are created using 3-D solid modeling software.
This detailed design work includes:
Determining the exact processes for manufacturing prototype parts
Determining the manufacturing tolerances will be for those parts
During this process, analysis and material science experts and engineers guide the selection of the specific materials that will be used. Any off-the-shelf components needed for the prototype are specified and sourced.

4 - PROTOTYPING
A prototype is an early version of an actual physical product. Not just a mockup, it is a working system that performs all or some of the intended functions of the final product.
For complex systems, it is common to first prototype parts of the complete system for testing and evaluation before a complete system prototype is developed.

5 - TESTING
Once prototypes have been constructed, it is time for testing to begin. The testing process determines how well the prototype performs its intended function. It also can involve demonstrating other important characteristics, such as safety and reliability.
Depending on the project, testing can be as simple as a subjective assessment of ergonomics, to thousands of hours of detailed data collection and analysis.

6 - DESIGN ITERATION
Design iteration is the process of designing, prototyping, testing, and then repeating these steps. Once the prototype has been tested, we take what we learned from testing to update the design.
Rather than an indication of a deficient development process, design iteration is a powerful tool that leads to the best possible product.
This important step takes a good product and makes it great.
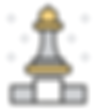
7 - DESIGN FOR MANUFACTURING
By necessity, the manufacturing methods used for making prototypes are typically different from the processes used for commercial production.
Examples include transitioning from 3D printing to injection molding for plastic parts, and transitioning from machining solid billet to castings for metal parts.
When prototypes are performing as planned, the process of transitioning to a manufacturable design begins.
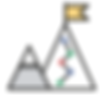
8 - PRODUCT LAUNCH
At this stage, you have completed your product - It's now time to launch it!
Begin production for the first round of the product launch. Evaluate how many products to produce based on your market testing and demand for the product. Advertise and speak to product distributors about ordering the product, if the product will be sold in stores.
Make sure you collaborate with a product developer who stays with you as long as needed, up to and through the launch phase. Working with a team of experts can allow you to take advantage of extensive manufacturing experience.
Product developers should be able to perform initial production runs, setup your production facility, or assist with setting up contract manufacturing.

9 - FIND AN EXPERIENCED PRODUCT DEVELOPMENT PROVIDER
There are many challenges and pitfalls when bringing a product to market.
Make sure to source a product developer who has a comprehensive and proven approach to nurture innovation while mitigating risk.
Inventherm offers turnkey product development services from concept to product launch.
From concept to completion, Inventherm has the skills and creativity to solve the most challenging problems.
We have experience with a wide range of technologies in a number of industries, including medical, consumer, and commercial products. Meet challenges with confidence and avoid costly mistakes.
Inventherm’s comprehensive and proven approach nurtures innovation while mitigating risk. Experience and dedication, coupled with in-house manufacturing capabilities allow us to rapidly develop products efficiently and cost-effectively.
